Automation – the path to efficient, future-proof manufacturing processes
.
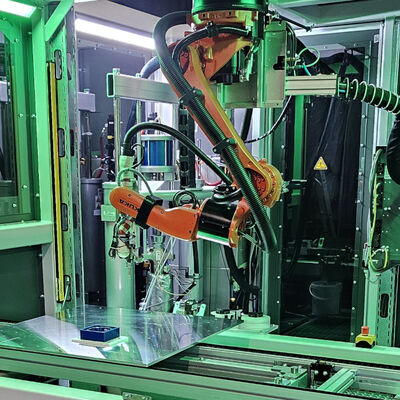
more efficient - resource-saving - reproducible
Thanks to our broad technology portfolio, we solve automation tasks from large industrial processes to solutions required in medium-sized companies. For this we rely on our own mechanical design, electrical design, software development, mechanical and electrical manufacturing.
Dosing and filling line
Dosing and filling line for microreactor vessels. In the system, the reactor vessels provided as bulk material are separated, fed to the metering module and automatically sealed after the filling process. An optical control system checks the actual fill level. Afterwards, each checked filled microreactor vessel is labeled and automatically cartoned.
Deburring plant
Machine for deburring thermoset frames for switches and sockets. Tool-related burrs in the inner contour and mounting surface are removed. The frames processed in the machine are installed by the user without further processing. The processing of different frames is possible by selecting the product in the user interface of the control without any set-up operations.
Manufacture SMD bridge
Fully automatic machine for the production of passive SMD jumpers. The system can produce different formats under software control. In addition to the production modules, the system contains 3 test stations for checking each manufactured workpiece. Electrical and geometrical parameters are checked. Thus, the manufactured components can already be packed in blisters in the system and directly fed to an assembly system at the PCB manufacturer.
Screwing machine
Automatic machine for the production of clamping pieces for the electrical industry. The clamps to be screwed as well as the screws are fed as bulk material so that the plant can produce without interruption. Each screwing process is monitored internally in terms of torque and angle of rotation.
Orbital riveting system
Automatic production of a orbital rivet joint for the manufacture of a component for a mechanical gearbox. The discs to be joined on the raw component are separated and positioned in the correct position in the riveting unit after visual inspection. The raw and finished components are transported within the plant by robots.
Universal test facility for vehicle components
Universally usable system for testing vehicle components. A wide range of pneumatic, mechanical and electrotechnical tests can be carried out. The test equipment is equipped with safety devices which protect the operator in case of destruction of test objects. The test facility was developed together with a manufacturer of special test software.
Manufacture of heat exchangers
Joining system and material supply for the manufacture of heat exchangers for gaseous media. The elements to be assembled are joined according to programmable parameters with a force of up to 20 kN, which can also be parameterized. During the automatic joining process, the operator prepares the next workpiece assembly to be manufactured. The final assembly can be removed using a load-bearing device.
Battery cooling module
Production cell for manual assembly of a battery cooling module for electrically powered trucks. The assembly sequence is monitored in every step. The data obtained in this process, which also includes the torques of each screw connection, is documented and transferred to a higher-level management system. After the assembly process, each module is tested in an automated in-house test facility. These test results are also permanently stored.
Automatic gearbox assembly
Automatic plant for the assembly of gearboxes for motor vehicles. The system is part of an interlinked production line. A wide variety of components are joined here, including pins, seals, springs and lubrication in addition to the functional elements. After the joining processes, all assemblies are subjected to an extensive testing procedure in a subsequent system so that they can be directly integrated into the production process at the vehicle manufacturer.
Surface inspection system
System for quality testing of highly stressed assemblies of power tools. The components to be tested are manufactured in very large quantities. To ensure reliable use of the finished products, components with the smallest surface damage and deformations must not enter the downstream process. An effective feeding system and high-resolution optical system detect defective components at very high speed.